汽車制造中沖壓板件就占了車輛重量50%以上,鋼板經過高速壓力機沖壓成為部品。內制部品在每一種車型中有100 點以上的部品都需要沖壓加工。從大件部品到小件部品,按照壓力機機械能力大小區分生產線。生產線構成有外板部品專用、外板部品與內板部品、以及內板部品等,生產中會發生形形色色的表面品質不良。按照沖壓板件的判定基準不盡相同,有必要對沖壓板件的品質按照客戶的需求進行生產。
外板部品與內板部品的不同文章源自好焊孫輝博客 http://www.4863x.com好焊孫輝-http://www.4863x.com/weldgyzb/autochongya202411279.html
沖壓板件分為內制部品與外部發注部品,外板部品與內板部品是不同的。外板部品(圖1)是指汽車外側部分所構成的部品,稱呼為外板板件。在成為完成車時,從外觀上看品質沒有影響;從專家的角度眼光看沒有不良。文章源自好焊孫輝博客 http://www.4863x.com好焊孫輝-http://www.4863x.com/weldgyzb/autochongya202411279.html
文章源自好焊孫輝博客 http://www.4863x.com好焊孫輝-http://www.4863x.com/weldgyzb/autochongya202411279.html
圖1 外板部品代表例,從左到右分別為發動機外板、門外板、尾門外板、側圍文章源自好焊孫輝博客 http://www.4863x.com好焊孫輝-http://www.4863x.com/weldgyzb/autochongya202411279.html
內板部品(圖2)是指汽車內側部分所構成的部品,稱為內板板件。成為完成車時,完全看不到的部分,以及有部分能看到(準外板)、因部品而異與限度樣品作比較來判定。文章源自好焊孫輝博客 http://www.4863x.com好焊孫輝-http://www.4863x.com/weldgyzb/autochongya202411279.html
文章源自好焊孫輝博客 http://www.4863x.com好焊孫輝-http://www.4863x.com/weldgyzb/autochongya202411279.html
圖2 內板部品代表例,從左到右分別為行李廂蓋內板、發動機內板、門內板文章源自好焊孫輝博客 http://www.4863x.com好焊孫輝-http://www.4863x.com/weldgyzb/autochongya202411279.html
評價區分的內容文章源自好焊孫輝博客 http://www.4863x.com好焊孫輝-http://www.4863x.com/weldgyzb/autochongya202411279.html
為了能夠正確客觀的評價車身,將車身品質判斷分為A 區、B 區、C 區,從三個不同的方向對車身的鋼板表面品質進行缺陷不良判斷(圖3)。文章源自好焊孫輝博客 http://www.4863x.com好焊孫輝-http://www.4863x.com/weldgyzb/autochongya202411279.html
文章源自好焊孫輝博客 http://www.4863x.com好焊孫輝-http://www.4863x.com/weldgyzb/autochongya202411279.html
圖3 車身品質判斷分區
A 區→車附近站立,不論是誰看,判斷都是不良。“非常員工評價”。
B 區→臉面從橫向觀測,不良比較薄。“嚴格評價”。
C 區→臉面更加往下觀測,不良薄。“稍為緩緩評價”。
具體缺陷問題判定基準與相應的對策
常見板件是有很多種缺陷,本文主要就車門外板表面缺陷問題進行探討(圖4)。
圖4 常見缺陷
壓痕(凹2)、麻點(凸)的原因和判定基準及對策
在沖壓生產過程中,壓痕、麻點(凹、凸)出現頻次比較高,很小的一些凹點、凸點難以被發現,噴涂后會造成光線紊亂和反射不規則,影響產品表面質量,也直接影響視覺效果,引起顧客不滿。造成沖壓過程中產生缺陷的因素很多,如:板材上異物、板材灰塵;模具沒有保養,拉延模具里的鋅粉、鐵粉等以及后工序模具刀口的碎屑未清理;HDA 裝置上的吸盤尚未清洗干凈,灰塵和雜物粘附在吸盤上。
⑴判定基準
①觸感:如圖5 所示,目視時,一眼就能發現的凹凸。
圖5 觸感
②用油石拭擦、底部幾乎不會留下油石的擦傷,而且凸的周邊僅留下少許油石的擦痕(圖6)。觸感確認的話1~2次能發現。
圖6 油石拭擦
⑵根據壓痕(凹)、麻點(凸)產生的原因進行對策,首先建立定期PM 保養體制,按照制定的周期計劃對模具開展保養。材料板件放置進行粉塵管理,生產前對吸盤、模具進行4S 擦拭及點檢管理。生產中根據生產狀況及時檢查模具切刀刃口的狀態。采用網格模技術(Cross Cut)這樣就可以有效減少壓痕(凹)、麻點(凸)。
起皺的原因和判定基準及對策
沖壓件起皺缺陷也是一種常見現象。產生根本原因是:沖壓模具上平衡塊間隙不一樣,在拉延時造成壓邊圈,局部對材料壓不緊引起起皺;拉延筋在高矮不一樣;頂料桿升起的高度不一樣,會導致局部壓料板松的地方起皺;壓力機的滑塊與工作臺平行度、垂直度超差;拉延過程中氣墊壓力過小,使成形過程中壓邊力不足,造成零件表面起皺。
⑴判定基準。
①觸感·目視時,一眼就能發現起皺。一眼就能發現判明是起皺,重疊不良。
②油石·觸感·目視時,容易發現。重疊不良建付沒有問題(重疊不良但沒有壓開裂)。
③觸感·目視時,不容易發現。使用油石檢查漸漸能夠發現,被認為是起皺。
⑵為了解決起皺缺陷方法如下。
①在產品設計中,盡可能降低翻邊高度,流動變形區域呈光滑狀態連接,適當減少板材的起皺;
②在沖壓生產工藝設計上,增大壓邊圈壓力,對進料速度進行控制;根據材料的流入量,在工藝上改善或增加圓形或方形拉延筋,依據材料流入量調整,來以防止起皺,面出現波浪;
③在材料的使用選擇上,對產品性能滿足的情況下,有些零件容易起皺,材料使用就應首先選用成形性較好的。
暗裂、開裂的原因和判定基準及對策
暗裂、開裂是沖壓材料在拉深過程中,材料應變超過其極限,而板件表面出現局部變薄、產生肉眼可見的裂紋、拉裂的現象。暗裂是沖壓零件重大的品質事故,在生產時,如果沒有被發現等裝車流出到市場,車輛在長時間行駛中會產生振動和異響,嚴重時甚至會影響車輛安全行駛、危及人員生命。
⑴開裂的主要原因分為三種類型:
①材料特性值有變化,如材料抗拉強度不足,材料變形量不足,材料有雜質引起裂紋,使零件開裂;
②壓力機氣墊的頂料桿頂出高度不一致,使模具壓邊圈所受壓力不均勻,材料流動時局部受力過大造成直接開裂;
③模具工藝存在設計缺陷,模具成形R 角過小,導致材料流動緩慢,容易引起材料開裂。(車門外板缺陷略圖見圖7.
圖7 模具工藝設計缺陷
⑵判定基準。
①板件開口、細腰拉延變大的(板厚減少1/3)NG。
②細腰拉延部分被承認但是板厚減少在20%~33%內也是NG。重要部品如強度部品需要檢查。
③表面粗造度過大,細腰拉延部分被承認但是板厚減少在20%以內。
⑶因此,預防暗裂、開裂主要包括以下幾個方面。
①調整板料的壓力,防止局部拉應力超過材料的實際抗拉強度。
②調整模具拉深間隙,使間隙分布均勻,以防止模具間隙不均勻引起的局部拉應力過高。
③適當增加模具凹模的圓角半徑,避免材料過度彎曲。
④調整模具溫度,對模具進行預熱或降溫處理,確保沖壓過程中材料受到均勻的溫度控制,減少由于溫度差異引起的開裂問題。
⑤修改模具設計,通過改變沖頭形狀、加強導向裝置或者增加襯套等方式來減少應力集中,從而有效減少開裂的情況。
⑥嚴格控制材料質量,采用化學成分、力學性能、延展性和成形性較好的材料,減少裂紋。
板件波浪產生的原因和判斷基準及對策
⑴沖壓材料在生產過程中可能出現波浪形,導致板材質量差(圖8)。造成這種現象的原因有很多因素:
圖8 沖壓材料在生產過程中出現波浪
①從材料因素方面來看,材料的塑性和厚度對沖壓件的成形有著重要的影響。塑性較差的或者厚度不均勻的材料就可能導致沖壓過程中出現波浪形狀。
②從模具設計方面來看,模具設計不合理,例如凹模圓角半徑過小,可能導致材料在塑性變形過程中流動速度不均勻,從而形成波浪。
③從模具使用磨損來看,長時間使用后模具表面的刃口和表面就會磨損,導致局部不平整,從而使沖壓件表面形成波浪。
④從沖壓速度來看,如果速度過快可能導致材料在模具內流動不充分,也會形成波浪。
⑤壓力分布不均勻會使材料在沖壓時流動不均勻從而導致沖壓件表面形成波浪。
⑵判定基準。
①觸感、目視下一眼就能夠發現。(圖9)
圖9 目視效果
②用油石、觸感、目視下容易發現的。
③觸感、目視下不是很容易發現,然而使用油石檢查漸漸能夠發現。
⑶為了減少波浪形貌的產生,我們可以采取相應的對策來減少或消除這種現象,經過綜合考慮各種因素并制定出一些科學合理的對策。
①材料的選擇:要選擇塑性好、厚度均勻的優質材料,使沖壓件的成形性得以提高。
②模具設進行計優化:合理設計凹模圓角半徑,使材料在塑性變形過程中的流動更加均勻。
③模具定期維護:對模具切刀刃口進行定期研磨和維護,以保持其刃口和表面平整光滑。
④控制沖壓速度:降低沖壓速度,以保證材料在模具內充分流動。
⑤調整壓力分布:通過調整模具結構和壓力機參數,使沖壓過程中的壓力分布更加均勻。
拉傷的產生原因和判斷基準及對策
⑴沖壓拉傷一般是指生產過程中,材料表面的拉傷、劃傷、撕裂等現象,如圖10 所示,拉傷原因也是有很多種因素:
圖10 沖壓拉傷
①材料表面有劃痕、雜質、裂紋等相關缺陷,或者材料的硬度、韌性等物理性能不符合要求,都可能導致沖壓拉傷。
②模具設計上不合理,如凹模圓角半徑過小、模具間隙不均勻等,會導致材料在沖壓過程中不能均勻流動,從而產生拉傷。
③模具的加工制造精度和裝配精度不良對沖壓件拉傷的影響也非常大。如果模具的間隙過大或不均勻,就會導致沖壓過程中材料流動不均勻,造成拉傷。
④潤滑劑可以減少摩擦,但如果使用不當,如涂抹過多或過少,或者使用了不合適的潤滑劑,可能導致沖壓過程中出現拉傷。
⑤操作工人在進行沖壓操作時,如果不按照規定的壓力機操作規程進行,如壓力調整不當、送料速度過快等,都可能導致沖壓件拉傷。
⑥壓力機閉合高度調整不正確、模具固定的不牢固等,都有可能導致沖壓過程中壓力不均勻,從而引起拉傷。
⑵判定基準
①從外觀上可以看見的NG(車門、行李廂蓋等、有包邊,有蓋的部品在打開時能夠看見)。
②包邊凸緣的翻邊面NG(發動機外板、門外板、尾門外板)。
③內板物件部品,沒有進行到撕開、開裂為止的程度。
⑶為了減少沖壓拉傷的發生,可以采取以下措施對策:
①提高、控制材料質量,采用力學性能、延展性和成形性較好的材料。
②在模具設計階段就要充分考慮沖壓件的形狀、尺寸、材料等因素,合理設計優化凹模、凸模、鑲塊等結構。選擇具有高硬度、高強度和高耐磨性的模具材料,同時,在制造加工過程中要采用先進的加工設備和工藝,提高模具的制造精度和光潔度。并進行適當的熱處理,可以提高模具的耐用性和抗拉傷能力。
③根據生產實際需要,選擇合適的潤滑劑并控制其用量,既要保證沖壓過程中的潤滑效果,又要避免因過量潤滑而引起的拉傷問題。
④對操作人員進行定期培訓和考核,提高他們的技能水平和安全意識,確保他們能夠按照規定的操作規程進行沖壓操作。
⑤此外,還需加強設備維護和保養、保持工作區域的整潔和安全也是減少沖壓拉傷的重要措施。
毛刺的產生原因和判斷基準及對策
毛刺也是沖壓件常見的問題。毛刺的產生不僅影響沖壓件的質量,還可能對生產過程造成困擾。
⑴沖壓件產生毛刺(圖11)主要原因:
圖11 毛刺
①材料本身的性能是產生毛刺的重要因素。材料的硬度、厚度、纖維方向等均可能影響沖壓過程中的毛刺產生。如硬度較高的材料在沖壓過程中更容易產生毛刺。
②模具設計不合理是產生毛刺的常見原因。例如,模具刃口的形狀、間隙、排樣方式等設計不當,都可能導致毛刺的產生。
③刃口磨損、崩刃或刃口間隙過大,都可能導致毛刺的產生。
④沖壓速度和壓力等參數設置不當,也可能導致毛刺的產生。
⑤潤滑油使用不當增加了模具與材料之間的摩擦力,材料在沖壓過程中溫度升高,沖壓件從而產生毛刺。
⑥模具和材料表面的污物和不潔,會增加沖壓過程中毛刺產生的風險。
⑦操作人員是否遵守規范也是影響毛刺產生的重要因素。
⑵判定基準。
①毛刺高度在0.5mm 以上NG。孔毛刺(一般孔)→密封孔、螺母焊接孔、W 基準孔、一般切斷面。
②毛刺高度在0.3mm 以上NG。角孔、長孔等(特殊孔)→夾緊孔、線束通過孔等。
③包邊面及安全上有問題的在0.3mm程度以下。
⑶根據使用目的不同,需要對現物孔徑公差(表1)進行確認。
表1 孔徑公差
⑷要減少毛刺的產生,需要從這些方面入手,綜合考慮并采取有效的措施。
①通過改進選擇適合沖壓的材料,并控制材料厚度和纖維方向。
②應充分考慮沖壓工藝要求,合理選擇模具材料,優化模具結構,以減少毛刺。
③應根據產品特點和沖壓工藝要求,定期檢查和更換刃口,合理調整刃口間隙,以降低毛刺產生的風險。
④當調整沖壓參數,如降低沖壓速度或壓力,可以減少毛刺的產生。
⑤使用合適的潤滑油可以減小模具與材料之間的摩擦力,降低材料在沖壓過程中的溫度,從而減少毛刺的產生。
⑥保持模具和材料表面的清潔,是減少毛刺的重要措施。
⑦加強操作人員的培訓和教育,確保他們熟練掌握沖壓工藝和操作規范,能有效降低毛刺的產生。
結束語
對汽車沖壓件表面品質不良的缺陷分析、判定基準的制訂及采取的對策,具有十分重要的意義。使相關人員對沖壓件表面品質不良缺陷產生的原因和對策有一個全新、全面認知。根據不同類型的沖壓件制定合適的沖壓工藝。在生產過程中,還需要綜合考慮各種因素,包括材料、模具、工藝參數等,制定出一套科學合理的生產方案。如選擇合理的壓邊力和SPM、適當的模具材料和凸、凹模尺寸。在模具設計過程中,改進了拉深筋的結構設計,提高了板料的成形性和穩定性。從而對沖壓件的表面質量進行有效控制,使整車的品質得到提升,造出“精品汽車”。
靳海峰, 趙磊, 張夢龍, 潘楨·廣汽豐田汽車有限公司
博主現就職于深圳市鴻栢科技實業有限公司, 從事焊接設備營銷推廣及銷售工作15年,擁有豐富的行業經驗及資源,致力于中國汽車焊接設備營銷推廣,歡迎廣大汽車制造焊接工藝與車身新材料連接技術研究的朋友們一起探討新技術、新設備。??
? ? ? ?螺柱焊機,點焊機,電極帽修磨機及各種焊接設備備件易損件,備件采購聯系:18682260315
AI賦能螺柱焊接系統:多模態感知、動態優化與自主決策的范式革新
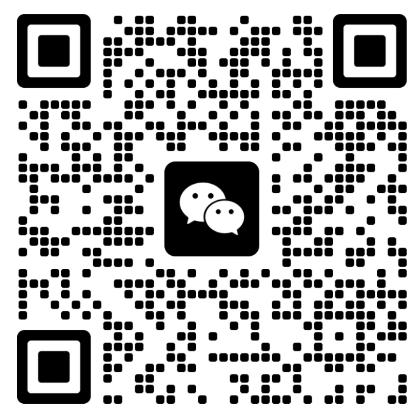