本文針對現場拼焊門內板開裂問題,結合模具狀態及開裂問題實際發生階段進行問題原因的查找,借用CAE 分析軟件進行穩健性分析驗證,篩選出重點影響因素,明確問題原因,針對性制定解決方案,并再次采用CAE 分析手段進行方案可行性驗證。本文對拼焊門內板開裂問題原因分析及整改方案制定進行詳細總結,為類似零件問題的解決給出分析思路和解決方法。
伴隨著汽車行業的迅猛發展勢頭,沖壓技術在汽車制造中的應用也得到了巨大的發展。汽車沖壓零件批量生產過程中的起皺、開裂等質量缺陷嚴重影響到沖壓線生產效率,并造成廢品率增高,生產成本增加。本文主要圍繞拼焊門內板批量生產過程中出現的拉延開裂問題,結合現場模具實際調試過程,借用CAE 模擬分析手段識別拉延成形開裂風險點、分析開裂問題產生原因并進行整改方案驗證,為拼焊門內板開裂問題的原因分析及問題解決提供了一種新思路。文章源自好焊孫輝博客 http://www.4863x.com好焊孫輝-http://www.4863x.com/weldgyzb/autoweld202411447.html
產品概況文章源自好焊孫輝博客 http://www.4863x.com好焊孫輝-http://www.4863x.com/weldgyzb/autoweld202411447.html
產品信息文章源自好焊孫輝博客 http://www.4863x.com好焊孫輝-http://www.4863x.com/weldgyzb/autoweld202411447.html
圖1 為前門內板結構圖,該車型所采用的拼焊門內板是一種材質為St06D +Z 的不等料厚激光拼焊板,厚板料的料厚為1.2mm,薄板料的料厚為0.65mm。文章源自好焊孫輝博客 http://www.4863x.com好焊孫輝-http://www.4863x.com/weldgyzb/autoweld202411447.html
文章源自好焊孫輝博客 http://www.4863x.com好焊孫輝-http://www.4863x.com/weldgyzb/autoweld202411447.html
圖1 前門內板結構圖文章源自好焊孫輝博客 http://www.4863x.com好焊孫輝-http://www.4863x.com/weldgyzb/autoweld202411447.html
板料信息文章源自好焊孫輝博客 http://www.4863x.com好焊孫輝-http://www.4863x.com/weldgyzb/autoweld202411447.html
板料為熱鍍純鋅拼焊板,牌號為St06D+Z-60/60,厚度為0.65mm/1.2mm,材料性能參數見表1。文章源自好焊孫輝博客 http://www.4863x.com好焊孫輝-http://www.4863x.com/weldgyzb/autoweld202411447.html
表1 材料性能參數文章源自好焊孫輝博客 http://www.4863x.com好焊孫輝-http://www.4863x.com/weldgyzb/autoweld202411447.html
文章源自好焊孫輝博客 http://www.4863x.com好焊孫輝-http://www.4863x.com/weldgyzb/autoweld202411447.html
生產開裂問題
在前門內板的現場批量連續生產過程中,拉延成形不穩定,在單批次批量生產300 臺(份)以上后,拼焊縫附近開裂(圖2)、縮頸問題不定時發生,嚴重影響正常批量生產,并且造成廢品率增加。
圖2 前門內板開裂區域示意圖
問題原因的分析
因前門內板開裂為批量生產時的偶發問題,針對本次問題原因計劃先借用CAE 分析軟件,從拉延成形性的理論分析結果入手,分析拉延成形安全裕度及穩定性,并針對性制定整改措施。
考慮現場實際,拉延調試狀態已與最初拉延工藝分析結果存在差異,為保證理論分析結果和現場實際狀態一致,對原始拉延模擬分析文件進行調整,保證理論收料線與現場實際狀態一致,進而再進行成形狀態確認。具體問題原因分析思路:現場拉延流入量檢測→拉延模擬分析優化→成形風險點識別→開裂影響因素分析→拉延穩健性分析驗證。
拉延板料流入量檢測
對生產過程中的門內板拉延件進行板料流入量測量并記錄測量結果,測量點位及測量方式如圖3 所示。
圖3 現場拉延板料流入量情況(單位:mm)
拉延模擬分析
按現場拉延實際板料流入量狀態調整拉延工藝,模擬分析拉延成形性,識別拉延成形性問題點。拉延板料流入量狀態見圖4,成形性分析結果見圖5。
圖4 拉延板料流入量狀態
圖5 拉延模擬分析結果
拉延成形風險點
從圖6 可以看出,位置1、2 處拉延成形減薄率過大,存在開裂風險;位置3 處拉延成形過程有褶皺趨勢,存在起皺風險,具體情況如下。
圖6 拉延成形風險點
位置1(圖7):減薄率24.2%超差,最大失效0.782 臨界,存在開裂風險。
圖7 位置1 模擬分析結果(原始)
位置2(圖8):減薄率23.3%超差,最大失效0.771 臨界,存在開裂風險。
圖8 位置2 模擬分析結果(原始)
位置3(圖9):成形過程褶皺,到底狀態指標未超差。
圖9 位置3 模擬分析結果(原始)
開裂影響因素分析
綜合考慮設備、板料及模具等波動因素,門內板開裂發生階段為大批量生產之后偶發的生產開裂問題,初步判定造成拉延開裂的主要因素為模具狀態波動。因為該門內板拉延模具采用了側推定位,板料定位狀態相對穩定,而模具隨著生產批量的加大溫度會增高,模具摩擦系數會發生波動,并且摩擦系數波動為主要影響因素,如圖10 所示。
圖10 開裂問題影響因素
拉延影響因素:穩健性分析驗證
針對摩擦系數波動對焊縫位置成形性的影響,采用AutoForm 軟件進行拉延成形穩健性分析,摩擦系數±10%波動,焊縫位置最大減薄率超過28%,最大失效為0.95,焊縫位置減薄率Cpk超差,廢品率增高。減薄率Cpk 結果見圖11,減薄/最大失效見圖12。
圖11 減薄率Cpk 結果
圖12 減薄/最大失效
拉延開裂問題整改方案
經過以上的模擬分析,拼焊門內板拉延成形安全裕度存在不足,模具狀態波動時會造成現場生產開裂,廢品率增加。其中摩擦系數波動為開裂問題的主要影響因素,從穩健性分析結果可以確認,摩擦系數降低可有效改善拉延成形的減薄率和最大失效,為解決摩擦系數波動引起的開裂問題可從降低拉延摩擦系數入手。
降低拉延摩擦系數的手段:⑴拉延模具鍍鉻(已采用);⑵板料涂油(不穩定);⑶更換板料鍍層(相對穩定)。針對拼焊門內板開裂問題,當前模具已是鍍鉻狀態,相對板料涂油措施,更換板料鍍層來降低摩擦系數能夠使生產過程更為穩定。本次問題整改采用更換板料鍍層方案,用鋅鋁鎂鍍層板料進行可行性分析驗證。
拉延工藝優化
采用鋅鋁鎂板料進行拉延模擬分析,鋅鋁鎂鍍層板料摩擦系數調整為0.13,其他模具參數保持不變,因摩擦系數降低,拉延四周整體多走料10mm。
圖13 為鍍鋅板和鋅鋁鎂板料收料線對比,為保證替換板料前后收料線一致,對工藝參數進行調整。從圖14 可以看出,壓邊力220t 保持不變,將圖示4條拉延筋加高1.5mm,優化拉延走料至原始狀態。
圖13 鍍鋅板和鋅鋁鎂板料收料線對比
圖14 工藝調整方案
拉延成形性模擬分析結果
根據現場實際板料流入狀態,調整拉延工藝的拉延筋高度,替換鋅鋁鎂板料、降低摩擦系數進行拉延成形性模擬分析;從圖15 可以看出,摩擦系數降低后,原焊縫位置開裂風險點的減薄率降低2%,最大失效降低0.2;通過替換鋅鋁鎂板料,使摩擦系數降低,可提高焊縫位置拉延成形安全裕度,說明此方案可行。
圖15 拉延成形性分析結果
位置1(圖16):減薄率21.8%,最大失效0.642;減薄率降低2%,最大失效降低0.15,安全裕度有所提升。
圖16 位置1 模擬分析結果(工藝優化后)
位置2(圖17):減薄率20.7%,最大失效0.544;減薄率降低3%,最大失效降低0.2,安全裕度有所提升。位置3(圖18):成形過程有起皺趨勢,到底狀態指標未超差;鋅鋁鎂板料成形過程與熱鍍鋅板料相差不大。
圖17 位置2 模擬分析結果(工藝優化后)
圖18 位置3 模擬分析結果(工藝優化后)
結束語
拼焊門內板開裂問題為實際現場批量生產過程中常見問題,針對現場已發生問題可借用CAE 分析手段進行問題查找及整改方案可行性驗證,可有效提高問題原因查找效率及整改方案的準確性,縮短現場整改周期、降低整改成本。針對該車型的門內板開裂問題,采用更換板料鍍層降低摩擦系數的方式,可有效提高拉延成形的安全裕度,避免因模具摩擦系數波動造成生產開裂、廢品率增加,為其他車型類似問題的分析、整改提供一種新的思路。
孫樹森, 李晶影, 代曉旭, 李建軍, 劉國磊·中國第一汽車集團有限公司
博主現就職于深圳市鴻栢科技實業有限公司, 從事焊接設備營銷推廣及銷售工作15年,擁有豐富的行業經驗及資源,致力于中國汽車焊接設備營銷推廣,歡迎廣大汽車制造焊接工藝與車身新材料連接技術研究的朋友們一起探討新技術、新設備。??
? ? ? ?螺柱焊機,點焊機,電極帽修磨機及各種焊接設備備件易損件,備件采購聯系:18682260315
AI賦能螺柱焊接系統:多模態感知、動態優化與自主決策的范式革新
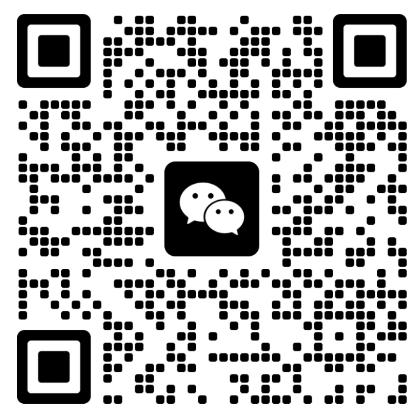